無電解めっきと電解めっきの違いをわかりやすく解説します
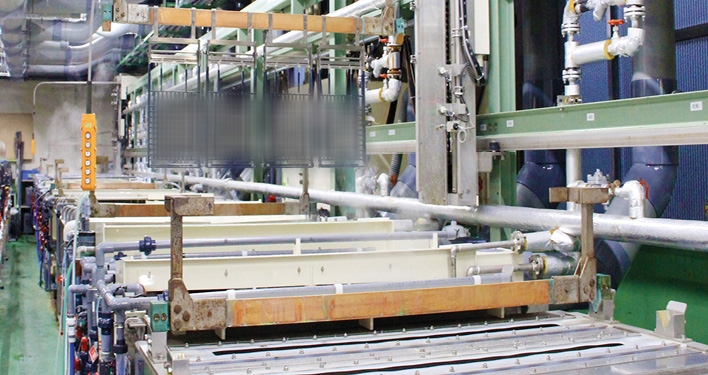
無電解めっきと電解めっきの違いについて
無電解めっきと電解めっきは、どちらも湿式めっきの一種で、基材表面に金属被膜を形成する方法として広く利用されています。
しかし、それぞれに特徴や工程の違いがあります。
無電解めっきは”金属の置換反応や還元反応”という化学反応を利用して均一な金属被膜を形成する方法で、電流を必要とせず複雑な形状の部品でも均一にめっきできます。
一方、電解めっきは電流を利用して金属を析出させる方法で、工程管理が容易かつ多様な用途に対応可能です。
このように、無電解めっきと電解めっきは特性に違いがあり、どちらかのみで処理することもあれば、混合工程で使用されることもあります。
当社では、これらの技術の両方に対応しており、お客様の多様なニーズに応じた最適なめっきプロセスを実施しております。今回のコラムでは、無電解めっきと電解めっきの違いについて詳しくご紹介します。
1.原理の違い
無電解めっきと電解めっきは、いずれも基材表面に薄い金属被膜を形成するための技術ですが、その原理には明確な違いがあります。
無電解めっきは、電流を使用せず、化学反応によって金属被膜を形成します。この方法では、めっき液に溶けた金属イオンが還元剤の作用によって還元され、基材表面に堆積します。
例えば、無電解ニッケルめっきの場合、めっき液中に含まれるニッケルイオンが次亜リン酸ナトリウムなどの還元剤によって還元され、基材表面に金属ニッケルとして析出します。この反応は、均一に進行するため、複雑な形状の基材でも均一なめっき層を形成することが可能です。さらに、導電性を持たない樹脂やセラミックスにも適用できる点が特長です。
一方、電解めっきは、電気を利用して金属イオンを還元させ、基材表面に金属を堆積させる方法です。このプロセスでは、めっき槽に基材を陰極として配置し、めっき液に金属イオンを含む溶液を用います。電源から電極に電流を流すことで、溶液中の金属イオンが基材表面で電子を受け取り、金属として析出します。この反応は、電流の強さや時間によって制御できるため、正確に層の厚みを制御可能です。ただし、電気を通す素材でなければこの方法は使用できません。
違いをまとめると、無電解めっきは化学還元反応に基づき、導電性を持たない基材にも適用できる柔軟な技術である一方、電解めっきは電解還元反応を用いて高精度で金属層を形成する技術です。
2.仕上がりや加工できる素材の違い
無電解めっきと電解めっきの仕上がりには明確な違いがあります。
無電解めっきは複雑な形状の基材でも均一な膜厚が得られるため、隙間や曲面にもしっかりとめっきが施され、全体的に滑らかで均質な仕上がりが特徴です。特に、耐食性に関しては電気めっきよりも高い性能を有しています。
一方、電解めっきは無電解めっきよりも、金属表面に光沢のある美しい仕上がりが得られるのが大きな特徴です。また、めっきする金属によって様々な特性を出すことができ、幅広い用途で使用されています。
ただし、複雑な形状では電流の分布が偏り、膜厚が不均一になる場合があります。
●無電解めっき、電解めっき特性表
加工できる素材においても違いがあります。前述したように、無電解めっきは導電性のないプラスチックやセラミックスなどの非金属にも加工が可能です。これにより、軽量化や複雑な形状の部品にも適用できるのが特徴です。
一方、電解めっきは加工対象が基本的に導電性のある素材に限られます。非金属素材の場合、直接めっきすることはできないため、無電解めっきを利用した下地処理が必要です。
これらの違いにより、適用分野や目的に違いがあるため、用途に応じて選択されます。
3.コストの違い
無電解めっきと電解めっきのコストには、それぞれの特性に基づく違いがあります。
無電解めっきは電源設備が不要である一方、化学薬品の使用量が多く管理が複雑になる場合があり、高性能な薬品を使用する場合は、コストが高くなることがあります。また、処理速度が遅いため、生産性がやや低下する場合があります。
一方、電解めっきは、導電性のある素材に限られるという制約があるものの、電力を利用することで効率的な処理が可能です。初期コストは電源設備が必要なため高くなる場合がありますが、長期間での運用コストは比較的安定しています。また、使用する薬品の種類や量も無電解めっきに比べて少ない場合が多く、全体的にコストを抑えることができる場合があります。
無電解めっきについて
前にも述べたように、無電解めっきは、電気を使わずに化学反応によって金属被膜を形成する技術で、非導電性素材(プラスチックやセラミックスなど)にもめっきが可能です。
原理は、還元剤を用いて金属イオンを対象物の表面に還元し、金属被膜を析出させるものです。反応が効率的に進むように、触媒処理によって対象物の表面に触媒(主にパラジウム化合物)を付与します。その後、めっき浴に浸すことで表面に均一な被膜が形成されます。
無電解めっきのメリットとデメリット
無電解めっきのメリットとして、非導電性の素材にも均一にめっきを施すことが可能で、複雑な形状や細かい凹凸がある素材にも均一な厚みでめっきを形成できるため、様々な素材に適用できる汎用性があります。このため、電子部品や医療機器など、高精度を求められる分野で広く利用されています。
一方、デメリットとしては、化学薬品の管理が必要で、薬品の劣化や廃液処理にコストがかかる点が挙げられます。また、電解めっきに比べて処理速度が遅く、生産性がやや低下する場合があります。さらに、薬品の調合や温度管理が工程の精度に影響するため、技術的な管理が重要です。
加工の工程
無電解めっきは、素材やめっき仕様によって必要な工程とその組み合わせに違いがあります。製品の数だけ存在すると言っても過言ではありません。まずは、無電解めっきで使用される工程をご紹介します。
A) 脱脂
加工時の研削油・潤滑油や汚れを除去します。
B) エッチング
表面の酸化膜の除去、表面の粗化を行います。表面が粗化されるとアンカー効果による密着性の向上につながります。
※アンカー効果…表面の微細な凹凸にめっきが入り込んで層の形成されることにより、めっき被膜と素材の物理的結合が強くなる効果。
C) スマット除去
表面上に残ったスマット(金属表面に残る合金物等の不溶解性の残留物)を除去します。スマットはめっき不良の原因になります。
D) 表面活性化
めっき直前の酸化膜と不純物を除去します。酸化膜や不純物はめっき不良の原因になります。
E) 触媒付与
素材表面に触媒を付与します。めっきの付きにくい表面への初期めっき析出を助けます。
F) 密着層(下地層)の形成
めっき密着性(素材とめっき被膜の密着力)を確保するためのめっき層を形成します。
G) 無電解めっき
H) 後処理
熱処理やコーティング処理
以上の(B)~(F)工程を素材に応じて選択・組み合わせで無電解めっきの工程は構成されます。
ここで“素材に応じて”ということについて補足させていただきます。もちろん、プラスチックや鉄、銅の素材によって工程が違うということでありますが、さらに、鉄の中でも、高炭素鋼や合金成分の違い、熱処理の工程の有無、そういった素材の違いでも工程が大きく変わるということを示しています。
無電解ニッケルめっきの加工工程
無電解めっきについて、無電解ニッケルめっきの例をいくつか挙げてご紹介します。
例①)鉄系素材Ⅰ
1. 脱脂
2. 表面活性化
3. 無電解ニッケルめっき
例②)鉄系素材Ⅱ
1. 脱脂
2. エッチング
3. スマット除去
4. 表面活性化
5. 密着層(下地めっき)の形成
6. 無電解ニッケルめっき
例③)銅系素材
1. 脱脂
2. エッチング
3. 表面活性化
4. Pd付与
5. 無電解ニッケルめっき
例④)プラスチック素材
1. 脱脂
2. エッチング
3. Pd付与
4. 無電解ニッケルめっき
以上、4つの例を示しました。このように素材やその組成、要求仕様によって必要工程やその順序に違いがあります。数多ある素材に対して、工程を構築するプロセスを迅速かつ正確に組むには、技術力・ノウハウ・加工経験が必要不可欠と言えるでしょう。
電解めっきについて
前述の通り、電解めっきとは、電気を用いて素材表面に金属層を形成する技術です。
原理としては、回路に電気を流すことにより、陽極またはめっき液中から金属イオンが陰極(素材)表面に溶解・移動し、表面で電子を受け取り還元され、金属として析出します。
電解めっきは、無電解めっきとは違い、素材をより平滑な表面へ近づける(レベリング性)という特性を持ちます。そのため、光沢のある美しい表面の形成、平滑性のある表面の形成に用いられます。
また、付与するめっきする金属によって、表面硬度の向上や耐摩耗性の向上等、様々な機能性付与用途でも用いられます。
※得られる機能性については、「無電解めっき、電解めっき特性表」をご覧ください。
電解めっきのメリットとデメリット
電解めっきのメリットとしては、前述の通り、光沢のある美しい装飾加工や平滑性や耐摩耗性向上のための機能性付与の加工が挙げられます。
また、大量生産を考えた場合、使用する薬品の種類や量が比較的少なく、浴の管理が簡単で、効率的にめっき処理を行うことができます。よって、長期的に見ると運用コストは安定的であることもメリットです。
デメリットとしては、表面上に凹凸があると凸部へ電気が集中、または、陽極との距離によってめっき厚が偏ってしまい、めっき膜厚を均一にすることは非常に難しいことが挙げられます。
加工の工程
電解めっきの加工工程は次の通りです。
まずは、無電解めっき同様に脱脂。次に、表面の酸化膜や不純物の除去のため、表面活性処理。その後、素材やめっきの種類にも依りますが、ストライクめっきや無電解めっきを用いて、密着層(下地層)として、めっき被膜を薄くつけます。(※下地に無電解ニッケルめっきを採用する場合は、脱脂以降の工程は素材に応じた無電解めっきの工程になります)
この工程は、ストライク処理、下地めっきやシード層形成等と呼ばれています。この処理を行うことで、めっき被膜と素材の密着性を向上させることができます。
その後、電解めっきを施します。また、無電解めっき同様、後処理として熱処理やコーティング等を行うこともあります。
めっきのご相談はスズキハイテックまで!
ここまで、無電解めっきと電解めっきの違いについて当コラムをご覧いただきましてありがとうございました。
当コラムでは、無電解めっきと電解めっきについて、それぞれの特性や違いに触れながら原理や使用用途、メリット・デメリットについてご紹介させていただきました。
弊社では、創業から111年の間、無電解めっき・電解めっきを用いて、様々な素材へ様々なめっきを行ってまいりました。そして現在は、その培ってきた技術を用いて、車載部品を始めとする高品質な大量生産を行っております。詳しくは、スズキハイテックホームページの“めっき技術”をご覧ください。
「めっきを用いて、装飾・機能性付与をしたい」や、「高品質なめっきを大量に生産したい」等のご相談ありましたら、下記お問い合わせフォームよりご連絡ください。
お問い合わせ先はこちら
電話番号:023-631-4703
お問い合わせフォーム